Ammonia is one of the most important and widely used petrochemical products and is the second synthetic substance with the chemical formula NH3, which is formed in nature from the decomposition of nitrogenous organic matter. The highest amount of ammonia consumption is in the production of fertilizers (urea, ammonium sulfate, ammonium phosphates). In the ammonia production unit, 8 catalysts are used to prepare the gas for the last reactor, which is responsible for the production of ammonia. The latest reactor is called ammonia synthesis. Smart Catalyst Company, which previously produced sulfuric acid catalysts, is now one of the companies that has taken an important step in the technical knowledge of ammonia synthesis catalyst production and has achieved this important production.
Magnetite-based iron catalysts with enhancers are commonly used. It has two types: structural (such as aluminum oxide, calcium oxide) and electronic (potassium oxide). Because it has a more active and suitable phase for ammonia synthesis. The main purpose of adding enhancers during the reaction is to improve catalytic activity, increase thermal resistance, help improve detoxification currents and increase the service life of catalysts. The activity of magnetite-based iron catalysts increases by only 2 to 3%, which makes the process more difficult. Some production units use non-ferrous catalysts, which is a good alternative to magnetite.
Magnetite type catalyst description |
||
Catalyst Type | SmartAM | SmartAM-Lord |
Particle shape | Irregular granules | Irregular granules |
Appearance | Black | Black |
Delivery Form | 60 liter Steel drums | 60 liter Steel drums |
Particle size, mm | 1.5-3, 3-6 ,6-12 | 1.5-3, 3-6 ,6-12 |
Surface Area, m2/g | – | 15 |
Bulk Density, kg/l | 2.6 – 3.0 | 2.1 – 2.4 |
Attrition Loss, %
Method: ASTM D-4058 |
< 2.5 | < 4.0 |
Chemical Composition (Nominal, wt. %) |
||
Fe, Fe Oxides | – | 94 ± 2 |
Fe Oxides | 94 ± 2 | – |
Al2O3, CaO, K2O, SiO2 | 6 ± 2 | 8 ± 2 |
In 1986, studies on iron catalysts with the Wustite precursor concluded that due to the greater activity of this catalyst during reactions and its high regeneration rate, it could be used to synthesize ammonia. Initially, it was produced under the brand name A301, but due to instability in its activities, researchers had to improve its formulation. Wustite iron catalyst is the most active type of molten iron catalyst for ammonia synthesis process. The most important additives of ferrous catalysts include Al2O3, K2O, CaO, etc.
Wustite type catalyst description |
||
Catalyst Type | SmartAW | SmartAW-Lord |
Particle shape | Granules | Granules |
Appearance | Black | Black |
Delivery Form | 100 liter Steel drums | 100 liter Steel drums |
Particle size, mm | 1.5-3, 3-6 ,6-12 | 1.5-3, 3-6 ,6-12 |
Bulk Density, kg/l | 2.8 – 3.2 | 2.4 – 2.6 |
Wustite type catalyst Composition (wt %) |
||
Fe, Fe Oxides | – | 83 Min |
Fe Oxides | 69 Min | – |
Al2O3, CaO, K2O, SiO2 | 6 ± 2 | 8 ± 2 |
Catalytic properties of ammonia synthesis
- High activity
- Long life
- Abrasion resistant
- High mechanical strength
- Minimal sensitivity to catalytic toxins
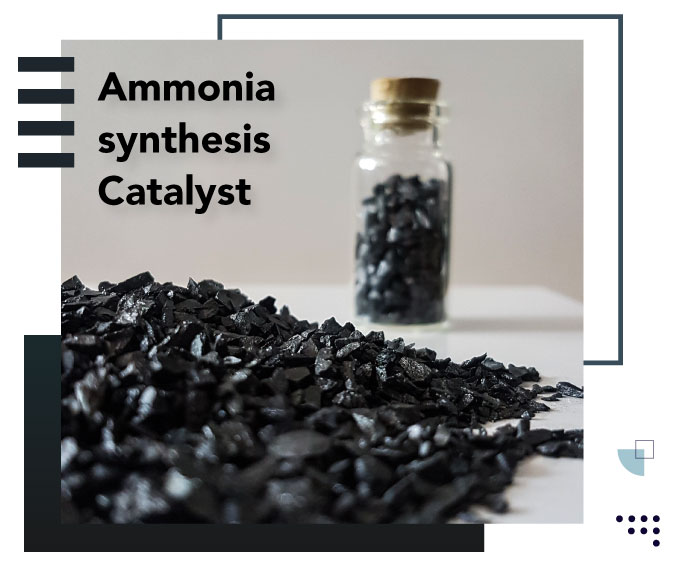
Use of SMART CATALYST in the production of ammonia synthesis catalyst
- Production of ammonia synthesis catalysts based on magnetite and wustite on industrial scales
- Perform all relevant tests and trials
- Performing reactor tests
- Accurate determination of the activity of ammonia synthesis catalysts
- Provide advice to ammonia units in order to select or replace the appropriate catalyst with their working conditions
- Update old ammonia units by performing corrective methods (catalyst, reactor and synthesis cycle)
Petrochemical Research and Technology Company is the highest reference in the field of testing, development and creation of technical knowledge of various petrochemical catalysts in Iran. Ammonia synthesis catalyst products in Smart Catalyst Company with the cooperation of the expert team of Petrochemical Research and Technology Company will be examined and after confirmation of physical, chemical and reactor specifications will be sent to the relevant petrochemicals. Ammonia synthesis catalyst samples produced by Smart Catalyst Company are produced by numerous reactor tests at temperatures above 2000°C, and by determining their physical characteristics. Ammonia synthesis catalyst manufactured by Smart Catalyst Company includes 4 types of ammonia catalysts: magnetite, reduced magnetite, and wustite and reduced wustite. In the following, we examine ferrous and non-ferrous catalysts.