Styrene is an organic compound, derived from benzene. It is the raw material of polystyrene and it is naturally found in small proportions in cinnamon, coffee beans, peanuts, Lawsonia inermis (Henna tree) and plastics, as well as coal tree. Producing styrene in industrial quantity is typically done by catalytic dehydrogenation of ethyl benzene.
This process was firstly performed in 1958 by Emory Petzer et al. at the Philips Petroleum Company. After production of sulfuric acid catalyst and ammonia synthesis catalyst by Smart Catalyst Company, we are proudly presenting an advanced catalyst which is produced by styrene monomer with remarkable performance, this product presents one of the most challenging usages in industry and provides the conditions for maintaining the economic benefits of the industry. Opting a catalyst that has high efficiency under SHR conditions can remarkably reduce the cost of production in factories. this catalyst that remarkably increases styrene production performance while reducing energy consumption and greenhouse gas emissions. Styrene is a synthetic chemical material which is used so as to produce various kinds of plastic. Since this material is widely used, Smart Catalyst has been able to reduce the environmental effects of styrene production by this catalyst.
Properties | Smart EBD4 | Smart EBD5 |
Shape | Circular column- Smooth | Circular column- Ripped |
Color | Chocolate brown | Chocolate brown |
Fe2O3, wt% | Matrix | Matrix |
K2O, wt% | Min.10 | Min.10 |
Promoter, wt% | Min.8 | Min.10 |
Attrition Loss, wt% | 1.5 | 2 |
L.O.I, wt% | 3 | 3 |
Size, mm | 3 * 4-6 | 3.5 * 4.5 * 4-6 |
Surface Area, m2/g | 2 – 3 | 2 – 3 |
Service cycle, Month | 24 – 36 | 24 – 48 |
Application | very high activity | New generation, high selectivity |
The properties of styrene monomer catalyst produced in Smart Catalyst Company
- High activity
- Long life span
- Abrasion resistant
- High mechanical strength
- Minimal sensitivity to catalytic toxins
- High conversion capability
- High selectivity
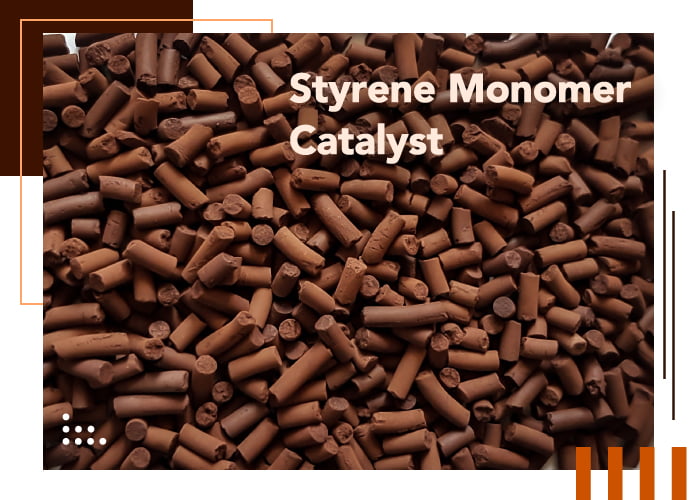
Services of the Smart Catalyst Company in the field of producing styrene catalyst
- Careful monitoring during the procedure and production process
- Performing relevant tests and experiments
- Performing reactor tests
- Specifying the exact level of activity and selectivity of ethyl benzene dehydrogenation catalysts
- Providing consultation to styrene units so as to choose or replace a catalyst proper to their working conditions
- Updating old styrene units by performing corrective methods (catalyst, reactor and synthesis cycle)
Smart Catalyst Company has been able to produce the most efficient styrene catalyst in Iran with highest activity and selectivity along with reducing costs and therefore increasing efficiency. Tests which have been performed demonstrate the strong performance of this catalyst. Thanks to its exclusive design, ethyl benzene (the ratio of vapor to hydrocarbon is also called SHR) achieves extraordinary activity and selectivity, at relatively low vapor conditions. The higher activity of catalyst increases the efficiency, while better selectivity reduces the by-products such as toluene and benzene, which usually have less value than styrene monomers. This issue is directly associated with economy and increasing efficiency for manufacturers and the petrochemical industry. Moreover, the optimal performance of the catalyst at SHR ratios makes styrene monomer production a more stable process. Particularly, the conversion process, which includes a new catalyst, consumes 82% less energy and reduces carbon dioxide emissions up to 79%.
1 Comment. Leave new
Greetings! Very helpful advice in this particular article! It is the little changes that will make the largest changes. Thanks for sharing!