اسید سولفوریک جز مواد پرکاربرد در صنایع مختلف است که به صورت مستقیم و یا غیر مستقیم میشود از آن استفاده کرد، به طوری که میتوان گفت معیار صنعتی بودن یک کشور به تولید و مصرف اسید سولفوریک وابسته است.
کارخانجات تولید کننده اسید سولفوریک از روش های مختلفی از جمله اسید سولفوریک تَر یا مرطوب (WSA, ECOSA)، اسید سولفوریک رقیق (Acidoura) و یا روش متابی سولفیت برای تولید این ماده استفاده میکنند اما یکی از شایع ترین روش ها، فرآیند تماس (Contact Process) است. در این مقاله سعی کردهایم در رابطه با روش تماسی برای کارخانجات تولید اسید سولفوریک گوگرد سوز که به عنوان یک روش عمومی شناخته شده است صحبت کنیم.
گوگرد ؛ ماده اولیه اسید سولفوریک
اسید سولفوریک با فرمول شیمیایی H2SO4 تشکیل شده از عناصر گوگرد، اکسیژن و آب؛ به طور معمول از طریق فرآیند تماس (مجاورت) یا تولید اسید سولفوریک به روش تر تولید میشود. از گوگرد به عنوان ماده اولیه برای تولید اسید سولفوریک استفاده میشود که به طور طبیعی در منابع نفتی و گاز یافت میشود؛ هم چنین از فرآیند تصویه فلزات نیز میتوان گوگرد استخراج کرد. روش تولید اسیدسولفوریک در کارخانه اسمارت کاتالیست به روش تماس مستقیم است که در آن از گوگرد خالص استفاده میشود.
ساخت و تولید اسید سولفوریک
فرآیند تولید اسید سولفوریک را میتوان به 4 بخش مجزا تقسیم کرد:
- استخراج سولفور (گوگرد)
- تبدیل گوگرد به دی اکسید گوگرد (SO2)
- تبدیل دی اکسید گوگرد (SO2) به تری اکسید گوگرد (SO3)
- تبدیل تری اکسید گوگرد (SO3) به اسید سولفوریک
-
تولید اسید سولفوریک به روش تماس
در این فرآیند ابتدا گوگرد برای تولید SO2 (دی اکسید گوگرد) سوزانده میشود. سپس با استفاده از اکسیژن و کاتالیزور پنتا اکسید وانادیوم طی یک واکنش گرمازا به تری اکسید گوگرد تبدیل میشود. در نهایت از ترکیب SO3 با آب، اسید سولفوریک به وجود میآید. این واکنش در دمای معمولی بسیار کند انجام میشود، به همین دلیل در تولیدات صنعتی در دماهای بالای 400-700 درجه سانتیگراد این آزمایش در حضور یک کاتالیزور مانند پنتا اکسید وانادیوم انجام میشود. در حال حاضر بالغ بر 50 شرکت تولید کننده اسید سولفوریک در ایران وجود دارند که تمامی آنها برای تولیدات خود از روش تماسی استفاده میکنند.
در کارخانه های شرکت ملی مس از خوراک گاز سولفوره که در واحد تشویه (Roasting) تولید شده، استفاده میشود که به این نوع از کارخانه ها، کارخانه های اسید سولفوریک متالوژیکی می گویند. کارخانه ذوب و روی بافق نیز از این نوع می باشد.
پالایشگاه آبادان نیز دارای کارخانه اسید سولفوریک با خوراک متفاوتی است. کارخانه اسید سولفوریک پالایشگاه آبادان از نوع بازیافت اسید سولفوریک فاضل می باشد که خوراک آن اسید سولفوریک ضایعاتی واحد بنزین سازی است که با سوزاندن آن، گاز SO2 لازم برای تولید اسید سولفوریک تامین می شود. مابقی کارخانه های اسید سولفوریک موجود در ایران مانند پتروشیمی رازی و کارخانه های خصوصی، گوگرد سوز هستند که از طریق سوزاندن گوگرد، SO2 لازم جهت تولید اسید سولفوریک را تامین میکنند.
-
بخش گوگرد مذاب و تولید گاز دی اکسید گوگرد
گوگردهای خریداری شده از پالایشگاه های گاز و نفت یا گوگرد معدنی؛ در حوضچه های مذاب توسط بخار به گوگرد مذاب تبدیل شده و سپس توسط پمپ های غوطه ور در استخر مذاب به کوره های گوگرد سوز اسپری میشود. در آنجا با اکسیژن حاصل از هوای خشک، سوخته و به گاز تبدیل می شود. هوای خشک مورد نیاز توسط بلوورها تامین شده و بعد از عبور از برج خشک وارد سیرکوله میشود، به دلیل اینکه اسید سولفوریک غلیظ در آنجا مدام در حال چرخش است، و در یک سیکل بسته قرار دارد به آن سیرکوله گفته میشود. در نهایت هوای خشک برای سوزاندن گوگرد به کوره انتقال می یابد.
گاز SO2 تشکیل شده در کوره ابتدا در دمای حدود 1000-850 درجه سانتیگراد میباشد که توسط مبدل های حرارتی WHB (ویست هیت بویلر) یا بویلر بازیافت حرارتی، به دمای حدود 450 درجه سانتیگراد کاهش می یابد، بعد از این مرحله وارد فیلتر شنی می شود. فیلتر شنی یک روش کاملا مرسوم در ایران بوده که در جهت جذب گرد و غبار حاصل از نسوزهای کوره و گوگرد واکنش نداده و جلوگیری از ورود آنها به بستر کاتالیستی استفاده میشود. ضمنا این فیلتر با توجه به مقدار سیلیس موجود در آن از بازه های دمایی احتمالی جلوگیری کرده و ظرفیت گرمایی بالایی دارد. در ادامه تصاویری از مبدل حرارتی WHB و فیلتر شنی مشاهده میکنید.
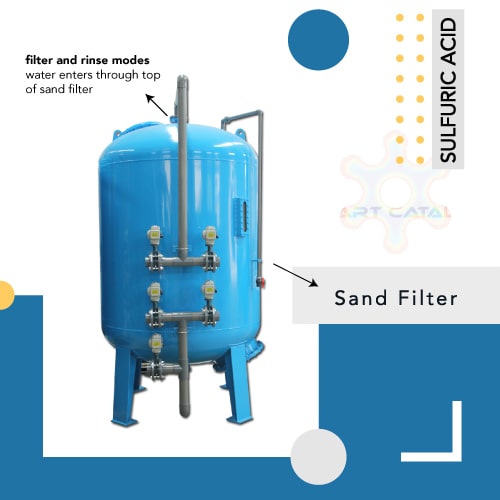
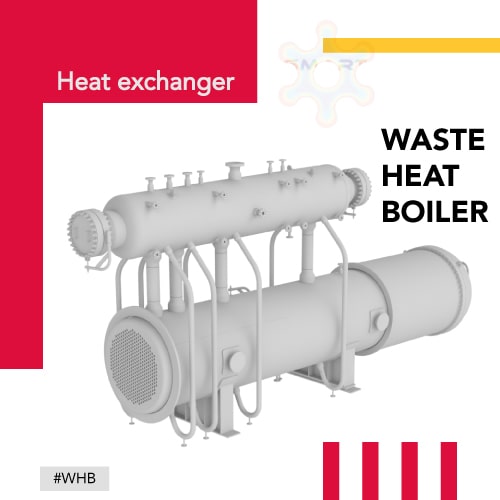
-
بخش راکتور کاتالیستی
گاز SO2 در دمای 420 تا 450 درجه سانتیگراد وارد بستر کاتالیستی میشود. با توجه به تناژ تولیدی، دبی گاز ورودی به کارخانه و غلظت SO2 تولیدی، راکتورهای کاتالیستی از 3 تا 5 بستر طراحی میشوند.
در ایران اکثر کارخانه های تک جذبی 4 بستره و کارخانه های دو جذبی به صورت 1+3 بستر یا 2+3 بستر یا 1+4 بستر ساخته شده اند. در طرح 3+1 که عمومی تر است گاز SO2 ورودی وارد بستر اول میشود، در این حالت تبدیل اولیه بسته به SO2 بین 50 تا 75 درصد امکان پذیر است. گاز دی اکسید گوگرد با اکسیژن موجود در گاز ورودی در کنار کاتالیست پنتا اکسید وانادیوم واکنش داده و تبدیل به تری اکسید گوگرد نمی شود. این واکنش به شدت گرما زا بوده و گاز خروجی از بستر کاتالیست از 420 تا حدود 600 درجه سانتیگراد افزایش دما خواهد داشت.
SO2+1/2 O2 → SO3+∆H
ابتدا این گاز توسط مبدل پوسته و لوله، خنک شده؛ سپس وارد بستر دوم کاتالیستی می شود. در این بستر فرآیند تبدیل گاز و دی اکسید گوگرد به تری اکسید گوگرد ادامه پیدا خواهد کرد که منجر به افزایش دمای حدود 70 درجه سانتیگراد خواهیم شد. این گاز نیز توسط مبدل بستر دوم خنک شده و به بستر سوم برگشته تا مرحله نهایی تبدیل که حدود 95٪ می باشد را انجام دهد. گاز خروجی از بستر سوم در کارخانه های تک جذبی با مبدل یا هوا، خنک شده و به بستر چهارم می رود و پس از اتمام توسط مبدل بستر چهارم به برج های جذب می رود.
در کارخانه های دو جذبی، SO2 بعد از بستر سوم توسط مبدل سوم خنک شده و گاز موجود در برج میانی توسط اسید سولفوریک غلیظ جذب می شود. مابقی گاز که حدودا 0.5 تا 1 درصد گاز SO2 دارد، بعد از گرم شدن توسط مبدل بستر سوم و مبدل بستر دوم، وارد بستر چهارم کاتالیستی می شود. در این بستر با توجه به مشکل به دما رسیدن و همچنین استارت آپ سخت، معمولا از کاتالیست پنتا اکسید وانادیوم سزیم دار استفاده می شود که در دمای حدود 360 تا 380 درجه سانتیگراد واکنش می دهد. بعد از بستر چهارم، گاز توسط مبدل بستر چهارم خنک شده و وارد برج جذب نهایی می شود.
-
بخش جذب گاز SO3
در برج های جذب، گاز SO3 توسط اسید سولفوریک غلیظ که بر روی پکینگ ها پاشیده می شود جذب شده و آب مورد نیاز آن در مخازن سیرکولاسیون تامین می شود. اسید تولیدی به مخازن ذخیره انتقال می یابد. اسید های خروجی از برج ها به دلیل بالا بودن دمای ورودی گازها، حدود 20 درجه افزایش دما خواهند داشت که توسط مبدل های استیل (که با حفاظت آندیک مجهز شده اند) خنک شده و به برج ها برگشت داده می شوند.
سوالات متداول
گازهای SO2 ناشی از سوزاندن گوگرد در تماس با یک کاتالیزور هستند به همین دلیل به این فرآیند روش تماس میگویند.
- وجودکاتالیست پنتا اکسید وانادیوم
- دمای حدود 450 درجه سانتی گراد
- فشار تقریبی 2 اتمسفر
این فرآیند در جهت تولید اسید سولفوریک انجام شده و یک واکنش برگشت پذیر و به شدت گرمازا است.
در این واکنش از پنتا اکسید وانادیوم (V2O5) به عنوان کاتالیزور استفاده می شود زیرا سرعت واکنش را افزایش می دهد و نیاز به دمای بالا را به حداقل میرساند. همانطور که در ویدئو توضیحات روش تماس بیان شد در این مرحله از فرآیند تماس، از اسید سولفوریک غلیظ برای حل محلول تری اکسید گوگرد تولید کننده اولئوم استفاده می شود.
سابق بر این از پلاتین به عنوان کاتالیزور این واکنش استفاده میشد. اما از آنجا که پلاتین حساس به واکنش با ناخالصیهای آرسنیک در مواد اولیه گوگرد است، اکنون اکسید وانادیوم ترجیح داده می شود.
دلیل اینکه نمیتوان SO3 را به صورت مستقیم در آب خالص ریخت این است که این واکنش بسیار گرمازا و انفجاری بوده به طوریکه پس از ریختن آب، محلول به شدت به اطراف پراکنده میشود. بنابراین باید به جای آن از محلول H2SO4 و آب استفاده کرد. بنابراین SO3 + H2O باعث تولید H2SO4 می شود.
فرآیند اتاق سرب و فرایند تماس از فرآیندهای مهم صنعتی است که برای تولید اسید سولفوریک در مقیاس بزرگ استفاده می شود. در هر حال فراگیری استفاده از روش تماس در کارخانجات به این دلیل است که این روش مقرون به صرفه است و در آن از کاتالیزورهای کم هزینه استفاده میشود. هم چنین این فرآیند باعث تولید تری اکسید گوگرد و اولئوم نیز می شود.