بیشتر مردم بوی تند آمونیاک (NH3) را با پاک کننده ها یا نمک های بویایی اشتباه میگیرند. با این حال، استفاده از این ماده در دو محصول ذکر شده تنها بخش کوچکی از کل تولید جهانی آمونیاک را نشان میدهد که در سال 2014 حدود 176 میلیون تن بود. برای اینکه بدانیم امروزه صنعت و فناوری تولید آمونیاک در چه سطحی قرار دارد؛ لازم است تا ابتدا نگاهی به چگونگی انجام این فرآیند بیندازیم.
آمونیاک بیش از 200 سال است که شناخته شده است. جوزف پریستلی، شیمیدان انگلیسی، اولین بار آمونیاک گازی را در سال 1774 جدا کرد. ترکیب آن توسط شیمیدان فرانسوی کلود لوئیس برتوله در سال 1785 مشخص شد. در سال 1898، آدولف فرانک و نیکودم کارو دریافتند که N2 را می توان توسط کاربید کلسیم برای تشکیل سیانامید کلسیم تثبیت کرد. سرانجام در سال 1906 فریتز هابر شیمیدان آلمانی به هماره تیمش، آمونیاک را در آزمایشگاه از N2 و H2 سنتز کرد.
تولید آمونیاک به روش هابر
تولید مقادیر قابل توجهی آمونیاک با استفاده از فرآیند سیانامید تا اوایل قرن بیستم اتفاق نیفتاد. از آنجایی که این فرآیند به مقادیر زیادی انرژی نیاز داشت، دانشمندان تلاش خود را بر کاهش انرژی مورد نیاز متمرکز کرده بودند. در همین حال، والتر نرنست، استاد شیمی فیزیک در دانشگاه برلین، فرآیندی را برای تولید آمونیاک با عبور مخلوطی از N2 و H2 از طریق یک کاتالیزور آهن در دمای 1000 درجه سانتی گراد و فشار 75 بار توسعه داد. او قادر به تولید مقادیر بیشتری آمونیاک در این فشار نسبت به آزمایشات قبلی هابر و دیگران در فشار اتمسفر بود. با این حال، نرنست به این نتیجه رسید که این فرآیند امکان پذیر نیست زیرا تولید تجهیزات بزرگی که قادر به کار در آن شرایط و فشار باشند، امری دشوار یا تقریباً غیرممکن بود (در آن زمان). با این وجود، هابر و نرنست هر دو مسیر سختی را برای تولید آمونیاک از طریق کاتالیزور دنبال کردند. هابر سرانجام فرآیندی را برای تولید مقادیر تجاری آمونیاک ایجاد کرد و در سال 1906 توانست به یک غلظت آمونیاک 6 درصد در راکتوری که با کاتالیزور اسمیوم بارگذاری شده است، دست پیدا کند.
فرآیند هابر یا هابر-بوش (Haber–Bosch process) توسط 2 شیمیدان آلمانی به نام های فریتس هابر و کارل بوش به صورت مشترک ابداع شد. به همین دلیل به این اسم نامگذاری شد. قبل از ابداع روش هابر تولید آمونیاک در مقیاس صنعتی امری دشوار بود. به طور مثال در روش های قبل تر (روش کارو) نیاز به مقدار زیادی نیروی الکتریسیته بود که هابر این مورد را در واکنش خودش حذف کرد.
تولید کود در تامین خوراک دو سوم جمعیت جهان نقش مستقیمی دارد. در قرن نوزدهم تقاضا جهت آمونیاک برای استفاده به عنوان کود نیتروژن بالا رفت. به همین دلیل هابر و تیمش دست بکار شدند. در این میان بوش ماشین رومیزی هابر را به ابعاد بزرگتر برای تولید در مقیاس صنعتی تبدیل کرد.
بیشتر بخوانید: تولید کاتالیست سنتز آمونیاک برای اولین بار در ایران توسط شرکت اسمارت کاتالیست
چالش اول: فراهم کردن شرایط مناسب برای انجام واکنش
واکنش پذیری نیتروژن بسیار ناچیز است به همین دلیل با هیدروژن در دما و فشار اتاق حتی در حضور کاتالیزگر هم واکنش نمیدهد. هابر در دماها و فشارهای مختلف با حضور کاتالیزگرهای مختلف این فرآیند را تست کرد تا بلاخره توانست شرایط بهینه را برای تولید آمونیاک محیا کند. هابر واکنش میان گازهای هیدروژن و نیتروژن را روی کاتالیزگر ورقهٔ آهنی (کاتالیزگرهای آهن و روتنیم) در دمای ۴۵۰ درجه و فشار ۲۰۰ اتمسفر انجام داد.
N2(g) +3H2(g) ⇌ 2NH3(g)
چالش دوم: جداسازی آمونیاک
اما به دلیل اینکه این واکنش یک واکنش برگشت پذیر یا تعادلی است؛ ابتدا هیدروژن و نیروژن آمونیاک رو تولید کرده و سپس مجددا آمونیاک به این دو عنصر تجزیه میشد. وی برای جداسازی آمونیاک از گازها، سرد کردن مخلوط را پیشنهاد داد تا با تبدیل آمونیاک به حالت مایع عمل جداسازی راحتتر انجام شود. برای اینکار از اختلاف نقطه جوش آنها استفاده کرد. (نقطه جوش آمونیاک 34-| نیتروژن 196- | هیدروژن 259-)
پس هابر دریافت که باید دمای واکنش را تا 40- درجه سانتیگراد پایین بیاورد تا آمونیاک به حالت مایع درآید. بعد از آن میتوان نیتروژن و هیدروژن را جداسازی کرد و سپس واکنش را دوباره به جریان انداخت تا عناصر باقی مانده نیز تبدیل شوند.
در حال حاضر از فرآیند هابر برای تولید صنعتی آمونیاک از نیتروژن و هیدروژن استفاده میشود. حذف مواد معدنی در مراحل تولید کود نیتروژن دستاورد فرآیند هابر بوده است که از آن به عنوان یک تحول اساسی یاد میشود.
این اتفاق به عنوان نقطه عطفی در توسعه یک فرآیند عملی برای تولید آمونیاک در مقادیر تجاری شناخته می شود.
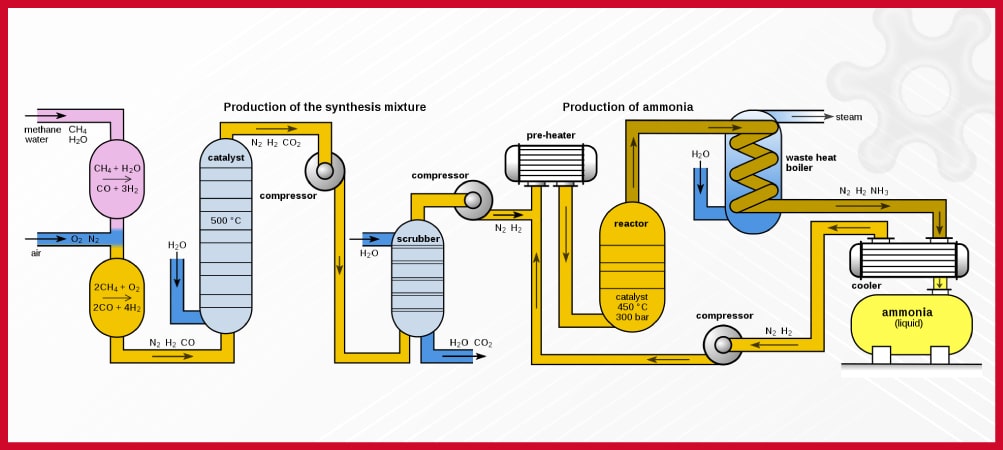
عناصر موجود در فرآیند هابر:
- کاتالیزور: اگر بخواهیم واکنش را بدون حضور کاتالیست انجام دهیم انقدر سرعت پایین است که عملا هیچ واکنشی اتفاق نمیافتد. با اینکه کاتالیزور در افزایش سرعت واکنش تاثیر مستقیم دارد اما در میزان حجم آمونیاک تولیدی نقشی نخواهد داشت. علاوه بر این، هنگامی که گازها از راکتور خارج میشوند دما و فشار بسیار بالایی دارند و این موضوع مانع تبدیل آمونیاک به حالت مایع میشود بنابراین باید دما را پایین آورد. با ترکیب آمونیاک با هوا در حضور کاتالیزور میتوان طی 3 مرحله نیتریک اسید تولید کرد.
- فشار: با افزایش فشار، روند تولید کاهش و سرعت واکنش گازها افزایش میبابد. افزایش سرعت منجر به برخورد مولکول ها و چسبیدن آنها به کاتالیزور میشود. اما انجام فرآیند در فشار بالا کاری هزینه بر است زیرا علاوه بر تامین تجهیزات و امکانات سخت افزاری، هزینه نگهداری و تعمیرات آنها را نیز باید در نظر گرفت. میزان فشار بهینه برای فرآیند هابر 200 اتمسفر تخمین زده شده است.
- دما: افزایش یا کاهش دمای واکنش رابطه مستقیمی با تولید فرآورده دارد. به دلیل گرماده بودن واکنش ممکن است روند انجام واکنش به سمت عکس برود. به همین دلیل باید تا حد امکان دما را پایین آورد. اما هرچقدر دما پایینتر باشد، سرعت انجام واکنش نیز کندتر خواهد بود. با توجه به اینکه هدف تولید بیشتر آمونیاک در مدت زمان کمتری است، به طور کلی دمای بین 400-450 درجه سانتیگراد مناسب اینکار میباشد.
- بازیافت: فرآیند هابر-بوش با مصرف 3 تا 5 % گاز طبیعی تولید شده در جهان؛ سالانه 450 تن کود در قالب آمونیاک، آمونیوم نیترات و اوره تولید میکند. جالب است بدانید مصرف آمونیاک به عنوان کود در کنار آفت کش ها باعث افزایش بهره وری در صنعت کشاورزی میشود. البته از خطرات این مواد نباید غافل شد. نفوذ نیترات ها به آب های رونده به سمت رودخانه و دریاها و سفره های زیرزمینی باعث تبدیل جریان آب به مرداب و کاهش کیفیت آب خواهد شد. هم چنین باعث انتشار گاز نیتروس اکسید N2O که به عنوان سومین گاز گلخانه ای شناخته شده است میشود.
هابر متوجه شد که مقدار آمونیاکی که در یک گذر از یک مبدل تشکیل می شود بسیار کم است و نمی تواند مورد توجه تجاری قرار گیرد. برای تولید آمونیاک بیشتر از گاز آرایشی، او سیستم بازیافت را پیشنهاد کرد و حق امتیازی را برای این مفهوم دریافت کرد. ایده بازیافت هابر درک مهندسی فرآیند را به عنوان ایستا به نفع یک رویکرد پویاتر تغییر داد.
هابر علاوه بر تعادل واکنش شیمیایی، سرعت آن واکنش را نیز که یک عامل تعیین کننده بود، تشخیص داد. به جای بازدهی ساده در طول یک فرآیند، او متمرکز بر بازدهی فضا-زمان در یک سیستم با بازیافت بود.
شرکت BASF پتنت هابر را خریداری کرد و توسعه یک فرآیند تجاری را آغاز کرد. پس از آزمایش بیش از 2500 کاتالیزور مختلف، کارل بوش، آلوین میتاش و سایر شیمیدانان BASF در سال 1910 یک کاتالیزور آهن ارتقا یافته برای تولید آمونیاک ساختند. توسعه تجهیزاتی که بتواند در برابر دما و فشار بالا مقاومت کند، کار دشوارتری بود. یک راکتور اولیه فولاد ملایم تنها 80 ساعت قبل از شکست به دلیل کربن زدایی دوام آورد. پوشش رآکتورهای فولادی نرم با آهن نرم (که در برابر کربن زدایی آسیب پذیر نبود) و افزودن شیارهایی بین دو آستر برای آزاد سازی هیدروژنی که در لاینر آهنی نرم پخش شده بود، این مشکل را حل کرد.
چالش اصلی دیگری که وجود داشت طراحی یک مبدل حرارتی برای آوردن ورودی بود. سرانجام اولین کارخانه تجاری آمونیاک بر اساس فرآیند Haber-Bosch توسط شرکت BASF در Oppau، آلمان ساخته شد. این کارخانه در 9 سپتامبر 1913 با ظرفیت تولید 30 متریکتن در روز راه اندازی شد. بعد از گذشته چند دهه، تولید آمونیاک در صنعت هم چنان از طریق روش هابر انجام میشود. در این واکنش که یک واکنش به شدت گرمازا بوده برای تامین هیدروژن مورد نیاز از گاز طبیعی متان استفاده میشود.

نسبت ترکیبات عناصر در واکنش
با هدف بهبود روند تولید، به کاتالیزور استفاده شده در این فرآیند مقداری پتاسیم هیدروکسید اضافه کرده تا توانایی بالاتری برای راه انداری فرآیند داشته باشد. درصد نیتروژن و هیدروژنی که در این فرآیند به راکتور وارد میشوند 1 به 3 است. در هر بار عبور گاز متان در طی فرآیند تنها 15% از N2 و H2 به آمونیاک تبدیل میشوند. با بازگرداندن هیدروژن و نیتروژن شرکت نکرده در واکنش طی یک چرخه دائم، در نهایت 98% از آنها به آمونیاک تبدیل میشوند.
تولید آمونیاک به یکی از مهمترین صنایع در جهان تبدیل شده است. بدون عملکرد محصول که توسط کودها و مواد شیمیایی مبتنی بر آمونیاک امکان پذیر شده است، جمعیت جهان حداقل دو تا سه میلیارد کمتر از امروز خواهد بود. تولید آمونیاک از سال 1946 به طور پیوسته افزایش یافته است (شکل 2) و تخمین زده می شود که با برخی از کارخانه هایی که بیش از 3000 متریکتن در روز NH3 تولید می کنند، ارزش تولید آمونیاک سالانه به بیشتر از 100 میلیارد دلار برسد.
تولید آمونیاک در سراسر جهان از سال 1946 تا 2014 به طور پیوسته افزایش یافته است.
سوالات متداول
تولید آمونیاک از طریق واکنش گاز نیتروژن و گاز هیدروژن و با استفاده از کاتالیزگر ورقه آهنی. این فرآیند نیتروژن هوا را با هیدروژن حاصل از گاز طبیعی متان ترکیب کرده و به آمونیاک تبدیل می کند.
- دما 400 تا 450 درجه سانتیگراد
- فشار 200 اتمسفر
- استفاده از کاتالیست آهن به عنوان کاتالیزور ورقه ای در این واکنش
2 دیدگاه. ارسال دیدگاه جدید
سلام مرسی از مقاله خوب و روان مختصرتون که اصل مطلب رو رسونده .
تو قسمت چالش دوم ، دمای جوش نیتروژن رو که نوشتین احتمالا مشکل تایپی بوجود اومده ، و 196- رو 169- نوشتید.
بعد از بررسی اصلاح کنید
با تشکر
درود بر شما
اصلاح شد