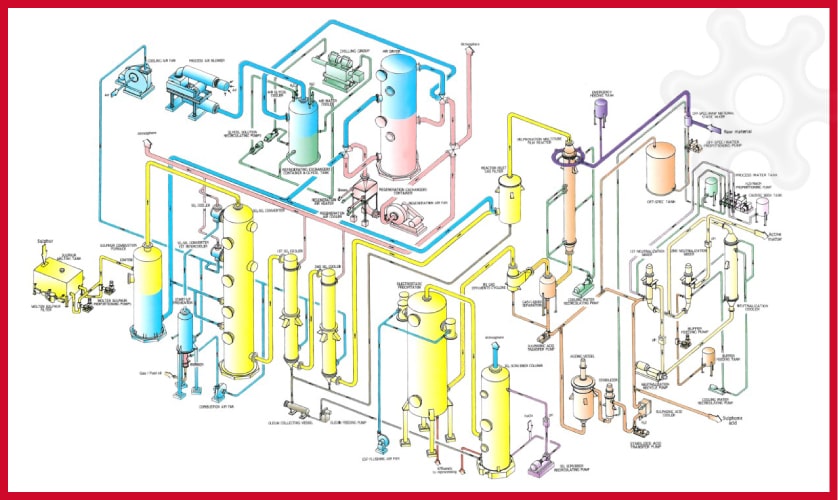
به طور معمول تولید اسید سولفونیک در میزان صنعتی به روش سوزاندن گوگرد می باشد. در این روش ابتدا گوگرد بصورت پودری یا کلوخه درون یکسری حوضچه های ذوب ریخته شده و در آنها توسط کویلهای بخار در دمای 130 درجه سانتیگراد ذوب می گردد. در آنجا ناخالصی های همراه گوگرد ته نشین خواهد شد و گوگرد مذاب بصورت سر ریز وارد حوض های ذخیره یا مخازن ذخیره بچر گوگرد خواهند شد. در این حوض ها یا مخازن، گوگرد توسط کویلهای بخار به حالت مذاب نگهداری میگردد. با كنترل فشار بخار و سیرکولاسیون مداوم جريان گوگرد مذاب، همواره دمای جريان كنترل می شود. در حقیقت وظیفه این حوضها، ذخیره مواد اولیه مورد نیاز است. سپس گوگرد مذاب توسط پمپ به داخل مشعلی درون کوره پاشیده شده و در محیط کوره می سوزد و تبدیل به گاز SO2 می شود (در حضور هوای خشك) و به این ترتیب گرمای بسیار زیادی تولید می گردد.
S + O2 → SO2 + Q
درجه حرارت كوره براساس غلظت گاز تولیدی پس از احتراق 600 تا 1000 درجه سانتيگراد خواهد بود. اين حرارت در مراحل بعدی نه تنها مورد نياز نبوده بلكه میبايست از سیستم دفع گردد. لذا با گذراندن گاز SO2 از داخل يك مبدل در بالای بستر 1 کانورتور یا ديگ بخار، درجه حرارت گاز به 420 درجه كاهش پیدا میکند و بدين ترتيب به ميزان زیادی بخار توليد میگردد. بطور کلی مشخصات بخار تولیدی وابستگی زیادی به نیاز یوتیلیتی این واحد و یا واحدهای جنبی خواهد داشت.
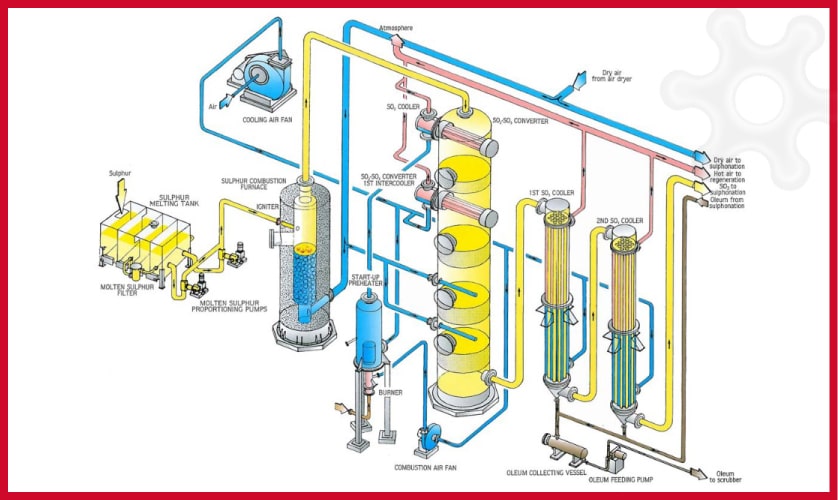
گاز خروجی با دمای 420 درجه سانتيگراد وارد اولين مرحله (بستر) از چهار مرحله كانورتور ميگردد. در اين مرحله تقريباً 60 تا 75 درصد گاز SO2 در حضور كاتاليست پنتا اكسيد واناديم به گاز SO3 تبديل ميگردد.
S+1/2O2→SO3+Q
اين واكنش نيز گرمازا بوده و دمای گاز تا 600 درجه سانيتگراد بالا میرود. جريان گاز پس از خروج از كانورتور طی گذر از يك مبدل هوا خنک یا اکونومایزر، به دمای 430 درجه سانتيگراد سرد شده و به بستر دوم كانورتور هدايت میگردد. در اين مرحه درصد تبديل SO2 به SO3 به 85% و دمای گازها به 510 درجه سانتيگراد میرسد كه ضمن خنک سازی تا 430 درجه سانتيگراد واكنش در بستر سوم كانورتور ادامه میيابد. درصد تبديل و دمای گازهای خروجی اين مرحله به ترتيب به 95-97% و 480 درجه سانتيگراد میرسد. ضمن سرد سازی مجدد جريان گاز تا 380 تا 420 درجه سانتيگراد، اين جريان به مرحله چهارم (مرحله آخر) كانورتور هدايت شده و با پيشرفت واكنش، درصد تبديل به 98% میرسد. 2 درصد باقيمانده كه قابل تبديل نيست به اتمسفر تخليه میگردد.

شما به هیچ عنوان نمیتوانید در شرایط عادی با ورودی دمای 420 درجه و با کاتالیست درصد بالا به زیر 1500 ppm دست یابید مگر اینکه از کاتالیستهای سزیمی و یا سوپر سزیمی استفاده کید تا موفق به کاهش رنج دما شوید. گفتنی است برای افزایش نرخ تبدیل، کاهش خروجی های محیط زیست، افزایش تولید و کاهش مصرف جاری سود سوزآور برای خنثی سازی گازهای خروجی باید دمای ورودی به بستر 4 را کاهش داد.
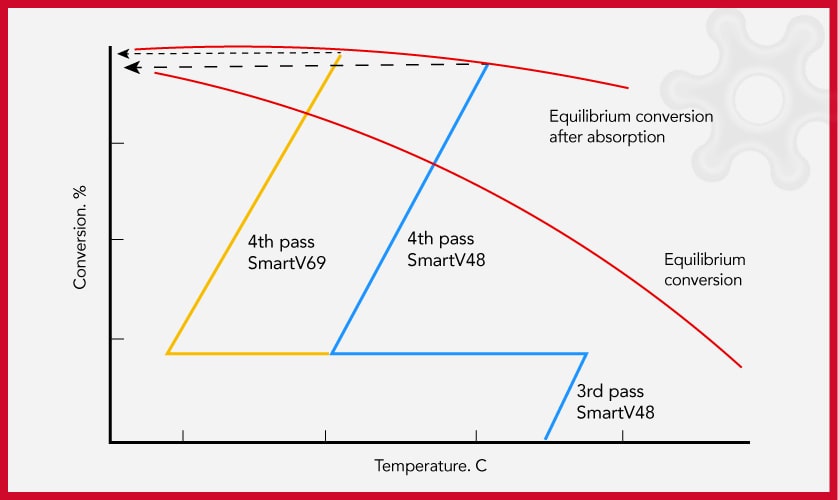
تصویر بالا نشان دهنده نمودار تعادلی برای سیستم تولید اسید سولفونیک و اسید سولفوریک در جهت مقایسه کاتالیست های سزیمی و معمولی است. هر مقدار که دمای ورودی به بستر 4 کاهش یابد، خط تبدیل به همان نسبت از نمودار تعادلی فاصله گرفته و تبدیل بیشتری انجام خواهد شد. با توجه به اینکه کاتالیستهای معمولی در دماهای زیر 420 درجه سانتیگراد خوب عمل نمیکنند باید از گریدهای مختلف کاتالیست سزیمی (SmartV69 یا SmartV59) در بسترهای 3 و 4 استفاده کرد. با استفاده از این نوع کاتالیست میتوان به شدت آلایندگی گاز خروجی را کاهش داد.
بیشتر بخوانید: انواع گریدهای کاتالیست اسید سولفوریک
جریان خروجی از بستر چهارم، می بایستی تا دمای 47-50 درجه سانتیگراد خنک گردد و این عملیات توسط دو دستگاه مبدل حرارتی هوا خنک یا اکونومایزر صورت میگیرد. این مبدل ها با هوا خنک میشوند. مبدل های حرارتی که وظیفه خنک سازی جریان گازی را دارند میتوانند بصورت بویلر و یا سوپر هیتر و یا اکونومایزر عمل نمایند.
جریان گازی SO3 وارد راکتورهای فالینگ فیلم شده و بعد از راکتور و ایجینگ، اسید سولفونیک تولید و به مخازن ذخیره انتقال داده میشود.
همچنین گاز واکنش نداده باید به فیلتر الکترواستاتیک منتقل شود تا قطرات سولفونیک یا LABS تولیدی حذف شود در غیر این صورت در اسکرابر باعث ایجاد کف شده و نمیتواند خوب عمل کند. گازهای دی اکسید گوگرد باقیمانده توسط اسکرابر حذف میشود. در اسکرابر از سود سوزآور استفاده میشود که هزینه های جاری زیادی برای مجتمع دارد. طبق برآورد کارشناسان فنی اسمارت کاتالیست میتوان گفت در صورتی که 10 درصد گاز ورودی تبدیل نشود؛ هزینه های جاری شامل گوگرد اضافی مصرف شده و سود سوزآور مصرفی برای حذف آلاینده ها در بازه زمانی 6 ماهه برابر با تعویض کل کاتالیست های واحد با بهترین نوع کاتالیست ها میباشد و در صورتی که این عدد حدود 20 درصد برسد این برابری به سه ماه کاهش خواهد یافت. تعویض کل کاتالیست ها در بازه زمانی کمتر از 6 ماه میتوان هم تولید با کیفیت داشت هم هزینه های جاری را به شدت کاهش داد و هزینه کل کاتالیست نیز برگشت داده خواهد شد. گفتنی است اکثر کارخانه های کنونی سولفوناسیون حدود 10 تا 20 درصد گاز ورودی را نمیتوانند تبدیل کنند.
2 دیدگاه. ارسال دیدگاه جدید
با سلام
عالی مختصر و مفید
سلام جناب صادقیان
ممنون از توجه شما